"The future isn't mass-produced; it's mass-personalized, empowering customers to co-create the products that shape their world." - Futurist Jim Carroll
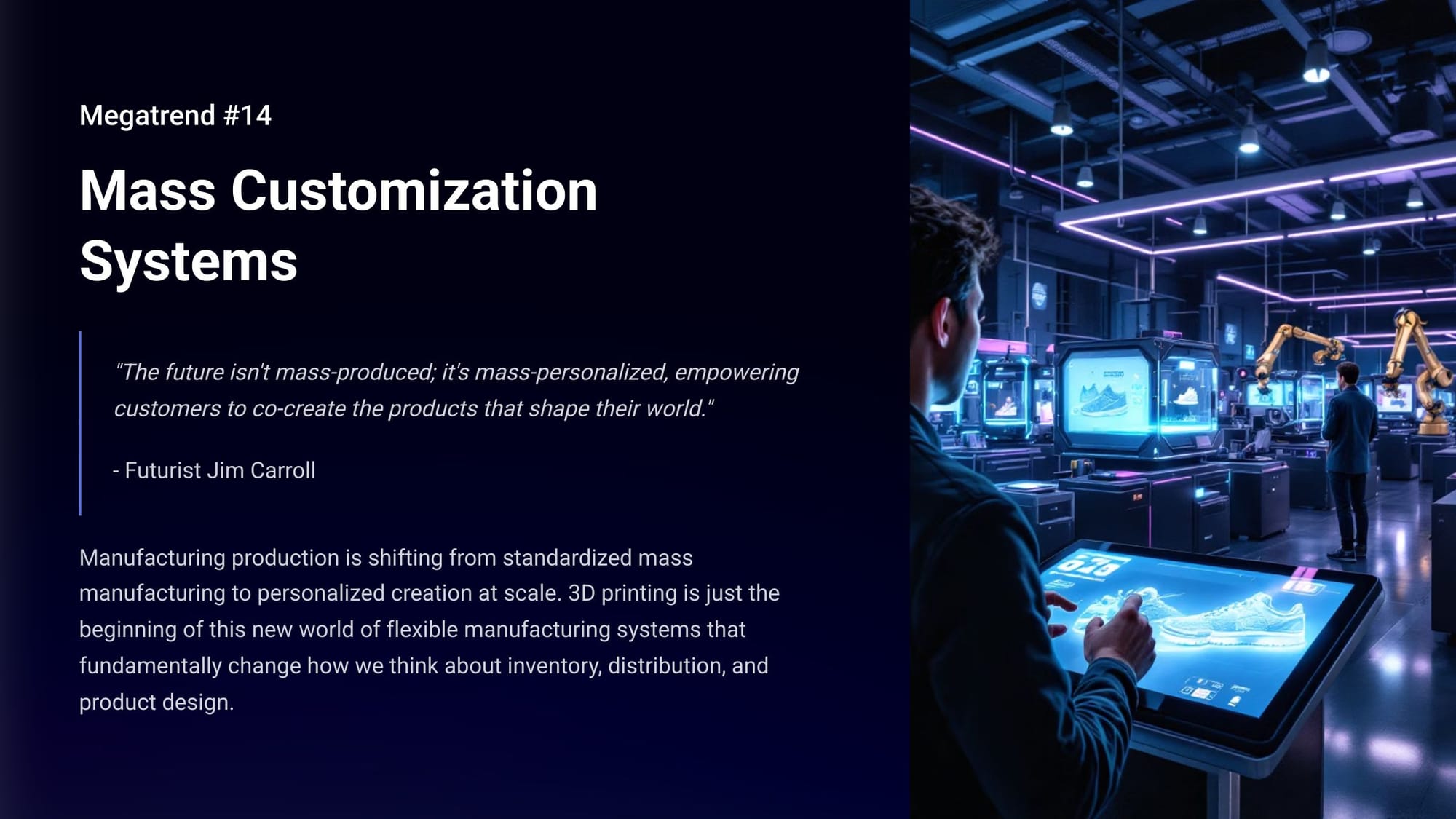
(Futurist Jim Carroll is writing a series on 30 Megatrends, which he first outlined in his book Dancing in the Rain: How Bold Leaders Grow Stronger in Stormy Times. The trends were shared in the book as a way of demonstrating that, despite any period of economic volatility, there is always long-term opportunity to be found. The book is now in print - learn more at dancing.jimcarroll.com)
It's time to shift gears - so far, this series has covered AI, energy, and healthcare - but now, with this trend #14, we'll shift into the manufacturing megatrend category:
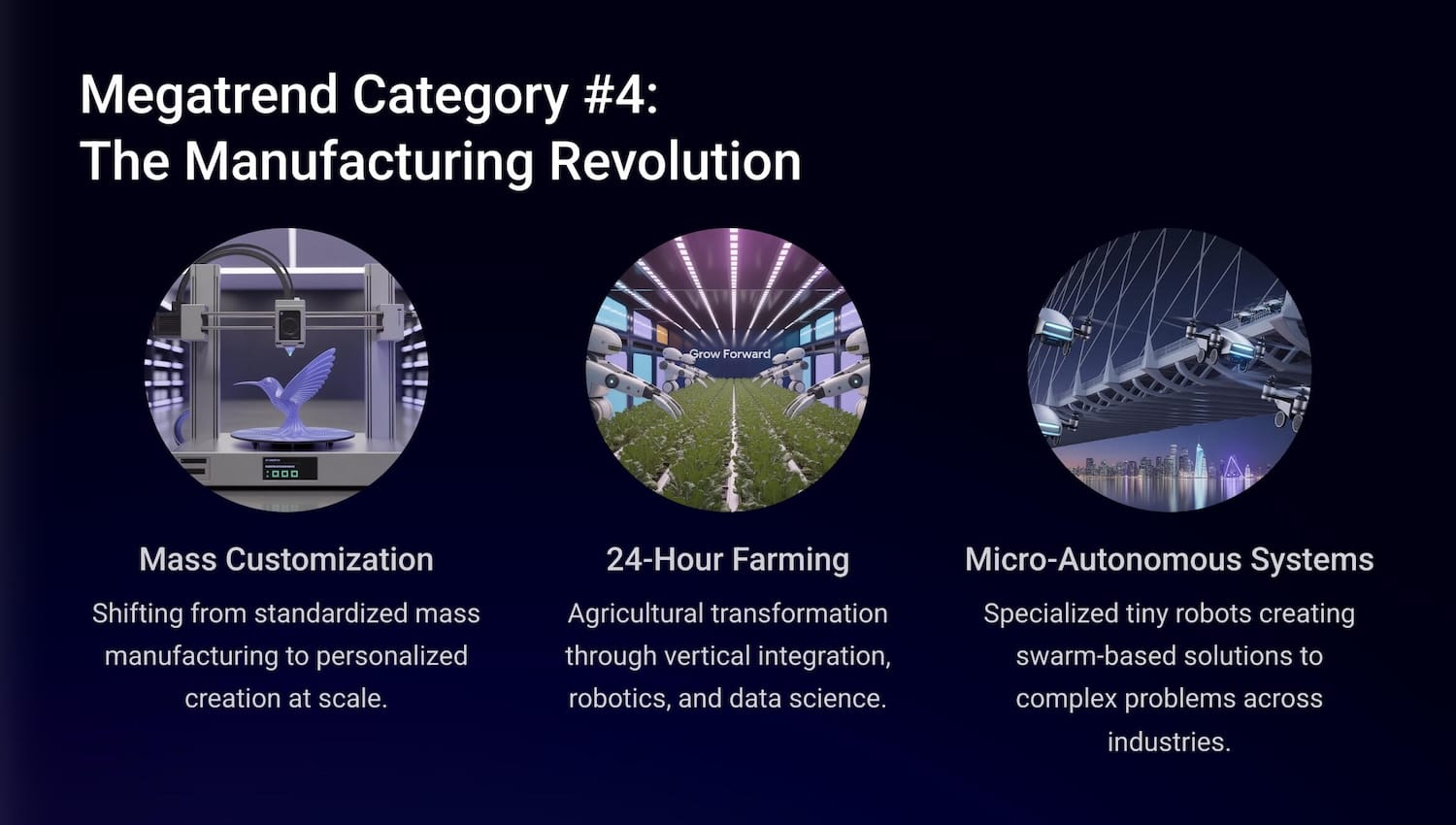
First up is 'mass customization.' What's that? Manufacturing production is shifting from standardized mass manufacturing to personalized creation at scale. 3D printing is just the beginning of this new world of flexible manufacturing systems that fundamentally change how we think about inventory, distribution, and product design.
As always, there's a full PDF right here - this blog post takes just a bit of that report and brings it in here.
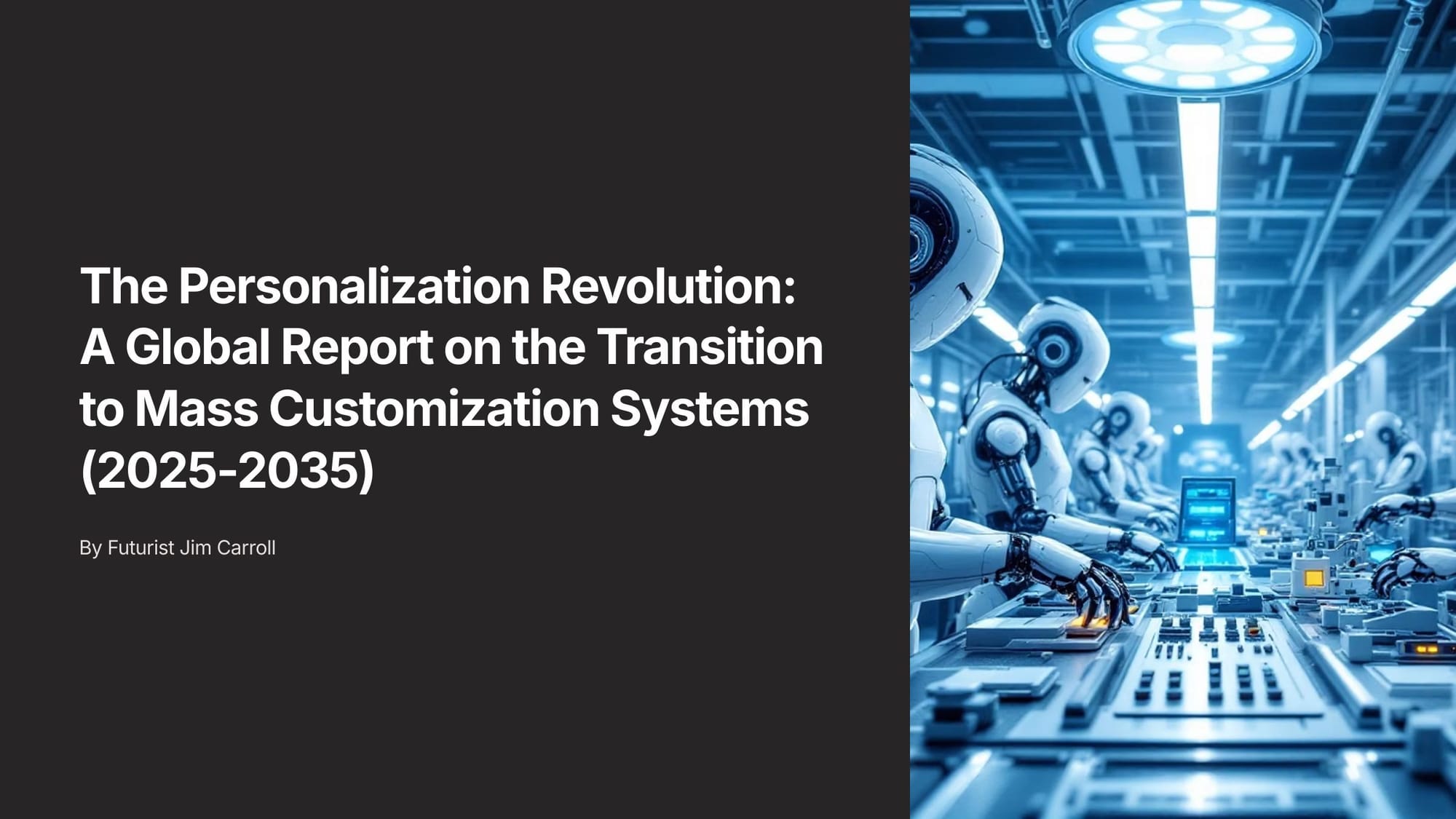
This is a rather tectonic shift, because manufacturing is moving away from the century-old paradigm of standardized mass production toward a more agile, customer-centric model: mass customization. This transition represents more than an incremental improvement in production techniques; it is a fundamental re-architecting of how products are designed, created, inventoried, and distributed.
Fueled by a convergence of digital technologies, new materials, and new methodologies, this new model promises to deliver personalized products at a scale and cost previously unimaginable, fundamentally changing the nature of competitive advantage and value creation in the 21st-century economy. (Success will also flow to those nations and regions that have the maturity to embrace the change. The rest will be pretty much behind and will see the end of most manufacturing jobs.)
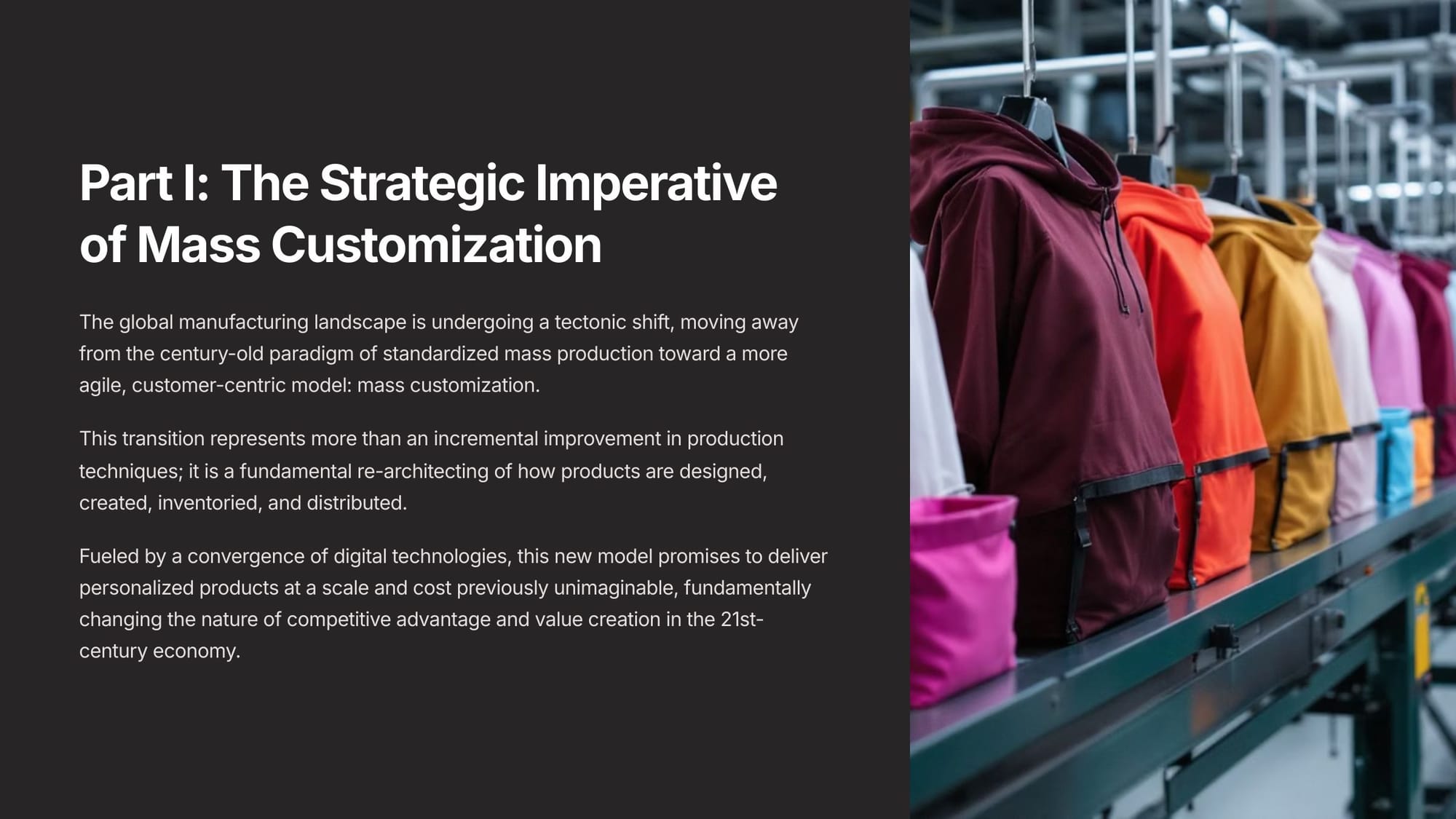
At its core, mass customization synthesizes the distinct advantages of two opposing production philosophies: the low unit costs of mass production and the high-value personalization of custom manufacturing. It involves a pretty dramatic shift from "make-to-stock to make-to-order."
That's a big change - traditional mass production "make-to-stock" models involve large batches of identical goods; mass customization inverts this logic by embracing "make-to-order" or "assemble-to-order" models, eliminating forecasting guesswork. A fundamental component of what makes this work is product design - deconstructing products into interchangeable components that can be produced efficiently in large quantities while allowing for vast customization possibilities.
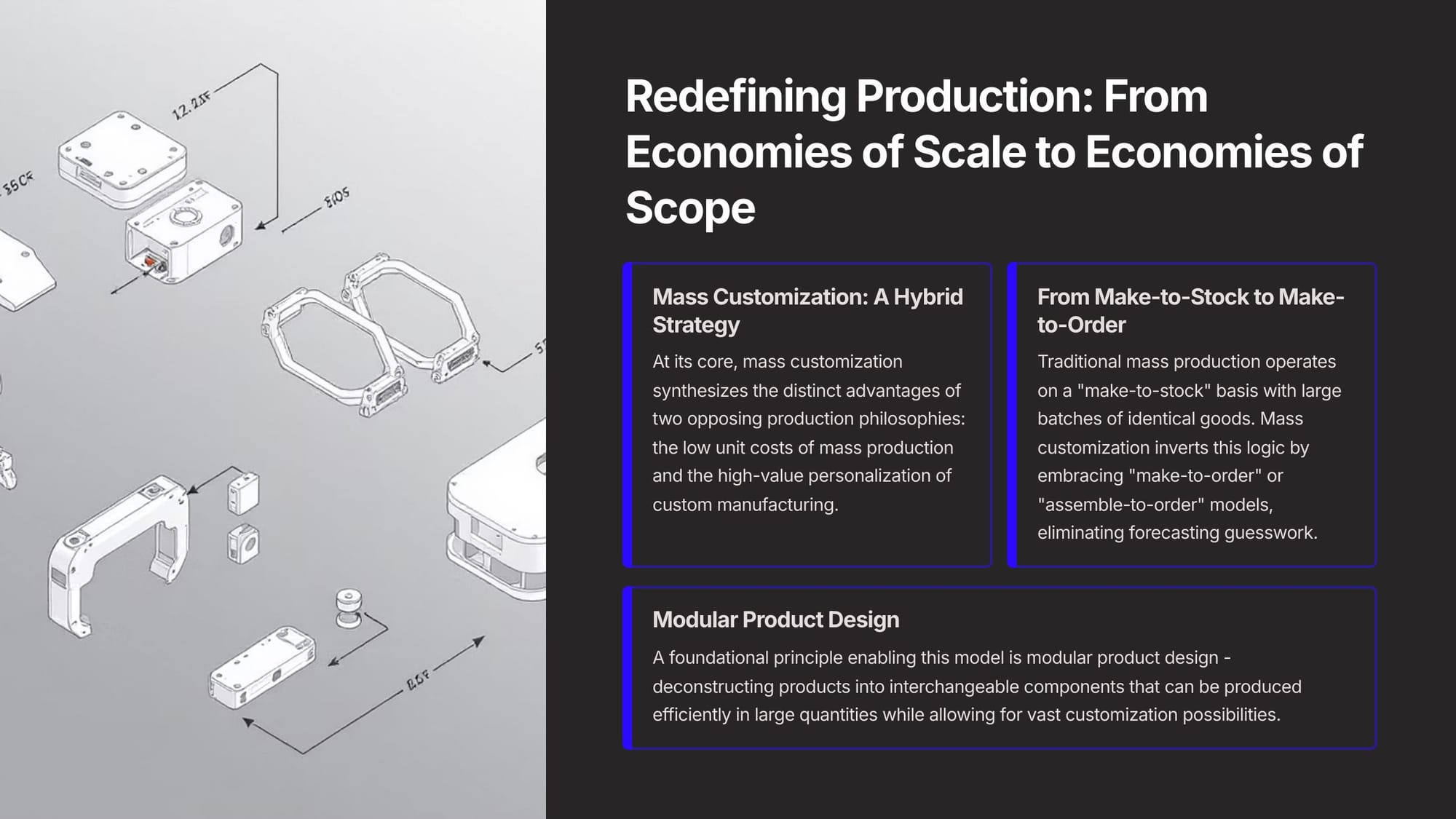
The adoption of mass customization triggers a cascade of transformative effects across the entire value chain, most notably in inventory management, distribution channels, and the nature of the customer relationship. By shifting from a forecast-driven to a demand-driven model, it fundamentally alters the flow of goods and information. The concept of inventory? It's from the olden days - the "make-to-order" approach dramatically reduces or even eliminates the need for costly finished goods inventory, aligning perfectly with Just-in-Time (JIT) manufacturing principles.
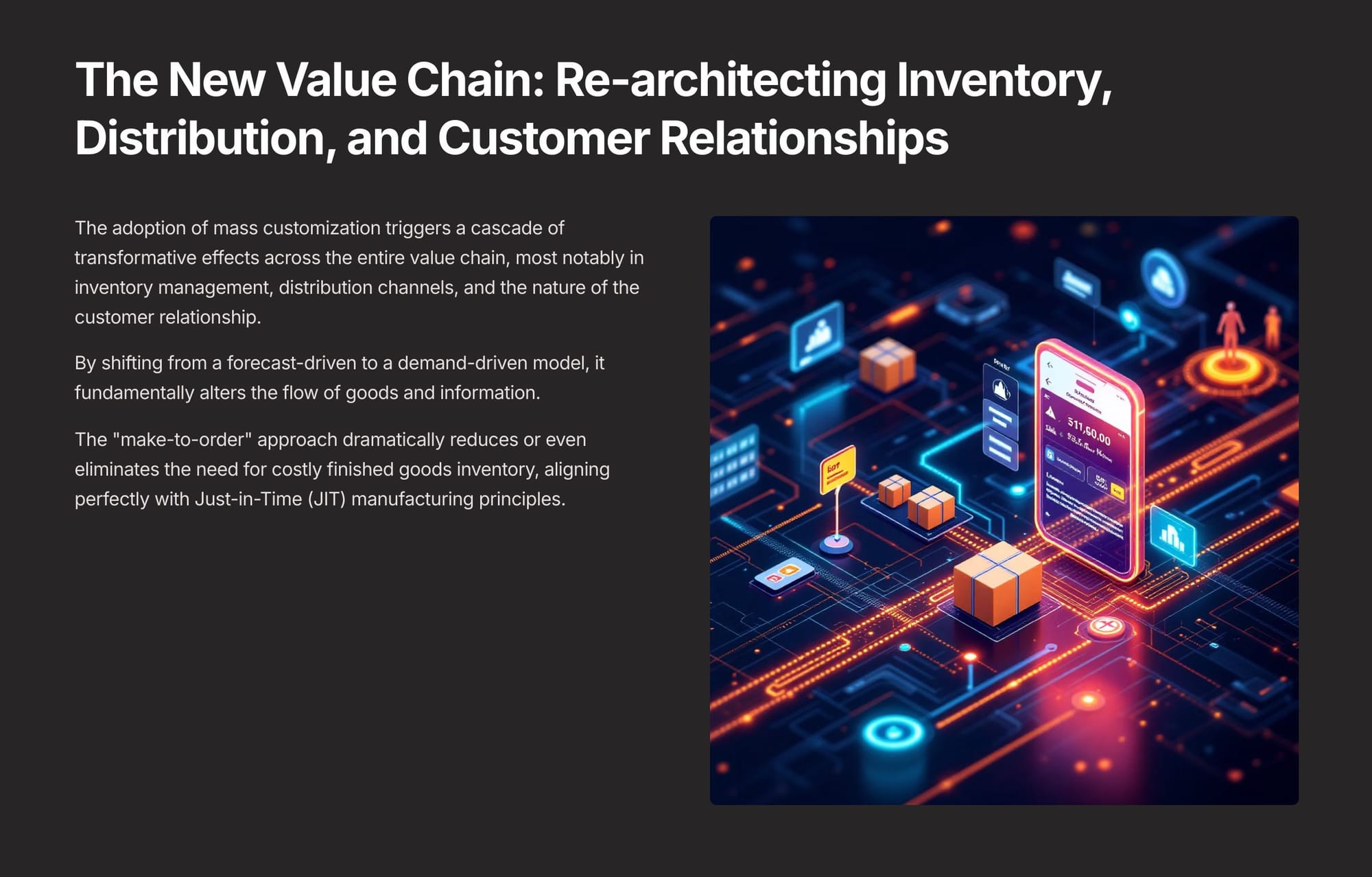
The trend itself is in line with the direct-to-consumer business model, which has become a key disruptive idea of the last few years, involving several components:
- Online Configurators. Web-based product configurators and mobile applications have become the primary sales channel, bypassing traditional retail intermediaries.
- Data Collection. Direct access transforms the supply chain into a two-way information highway, delivering valuable customer preference data back to manufacturers.
- Market Intelligence. Every customer choice becomes a data point that can be analyzed to identify market trends and optimize future product offerings.
- Experience-Centric. Companies shift from selling products to selling the experience of co-creation, fostering deeper brand loyalty.
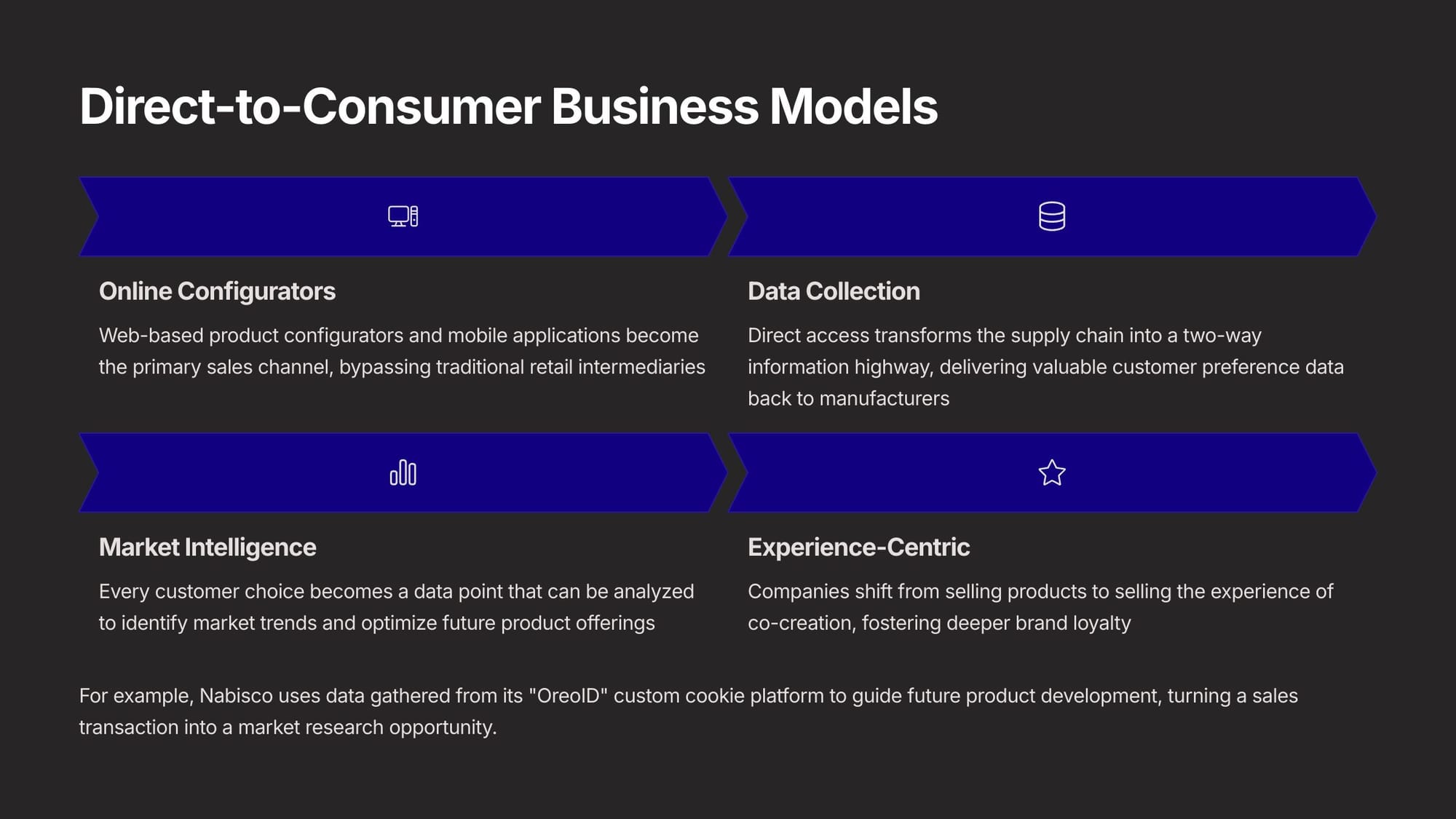
So what's behind all this? Mass customization is not the result of a single breakthrough but rather the convergence of a suite of advanced technologies. This "technology stack" forms a cohesive cyber-physical system that creates a seamless digital thread from customer input to final product delivery. This includes additive manufacturing (aka 3d printing), the flexible factory, robotics, and get ready - digital twin technology!
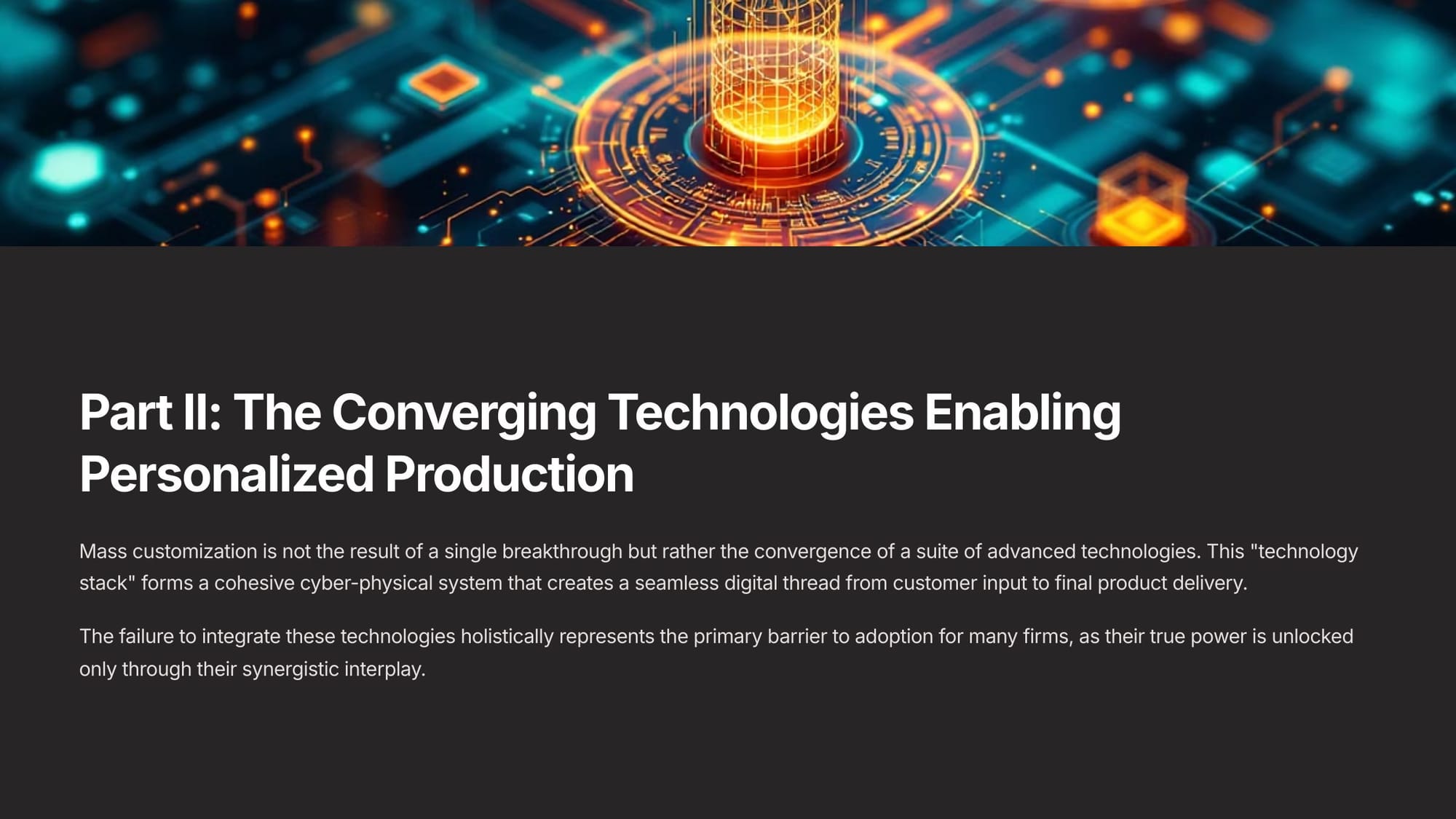
Additive Manufacturing (AM), commonly known as 3D printing, is arguably the most critical hardware technology driving the mass customization revolution. Its primary advantage lies in being a "toolless" fabrication process. Traditional manufacturing methods like injection molding require the creation of expensive, static molds, making it economically unfeasible to produce unique items in small quantities.
3D printing bypasses this constraint entirely. By building objects layer by layer directly from a digital file, a 3D printer can produce a completely different part with every run, with the only change required being the source CAD file.
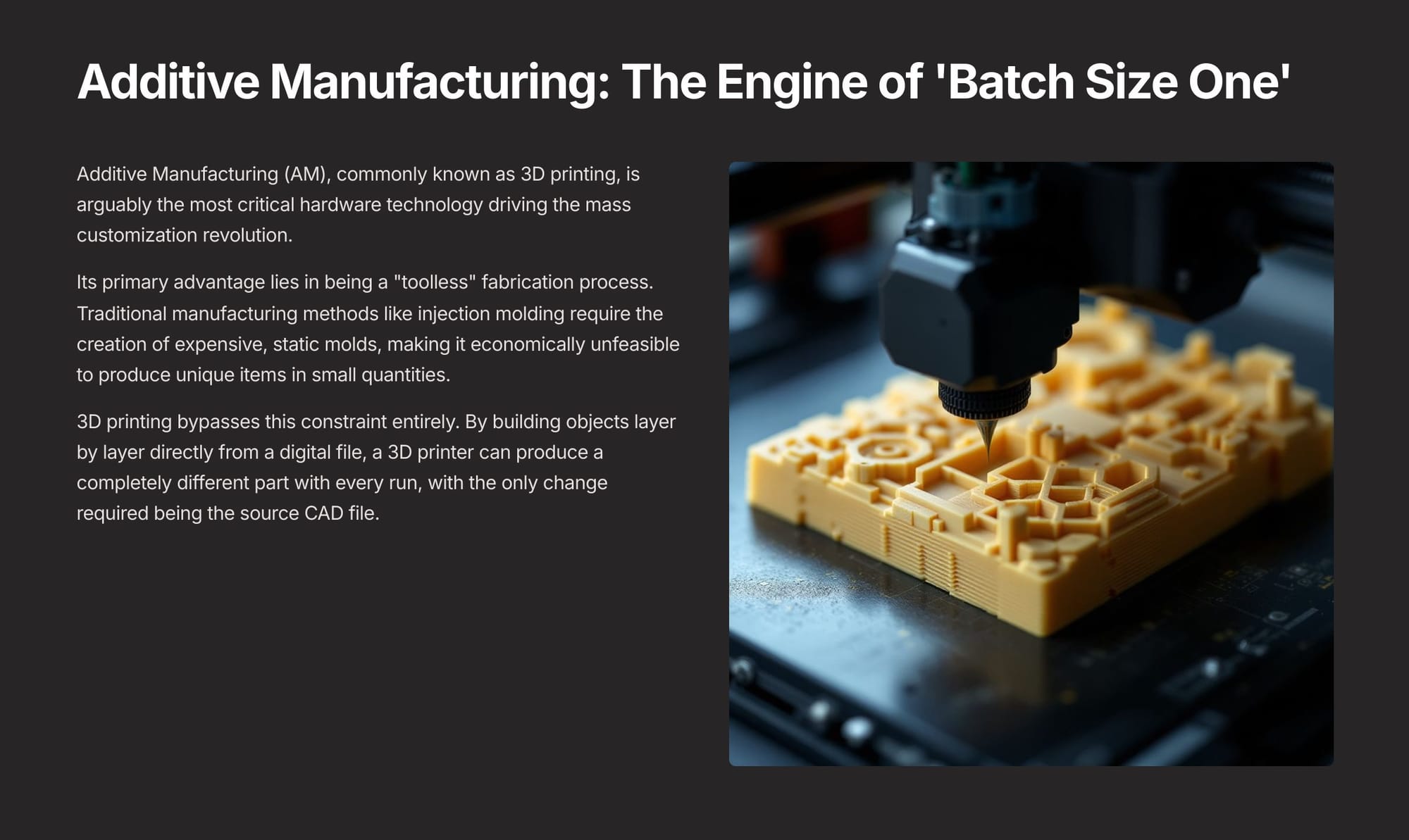
To produce a wide variety of customized products efficiently, the factory itself must be inherently agile. Gone is the idea of building an assembly line that will build a million products; in is an assembly line that will change itself to build one product.
This is achieved through Flexible Manufacturing Systems (FMS), which are designed to handle high-mix, low-volume production without costly downtime for changeovers. An FMS typically consists of reconfigurable cells of CNC machines, automated material handling systems, and a centralized control system that can dynamically route parts and adjust processes based on the specific order.
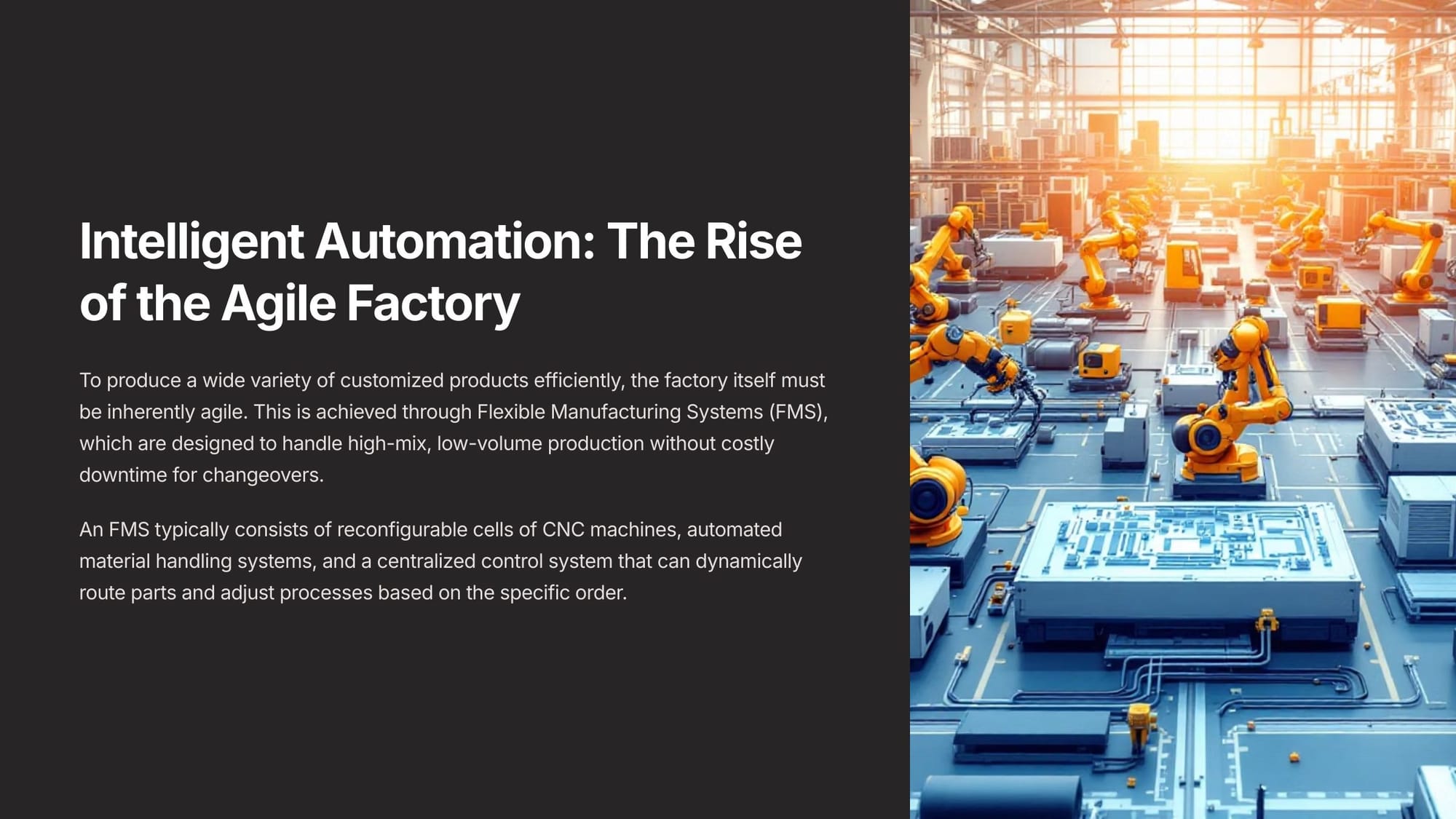
All of this involves the 'rise of the robots' and what we call 'collaborative robots' - robots that can work next to humans. : Unlike their traditional industrial counterparts, which must be isolated in safety cages, cobots are equipped with advanced sensors, force-limiting technology, and AI-driven motion control that allows them to work safely near human operators.
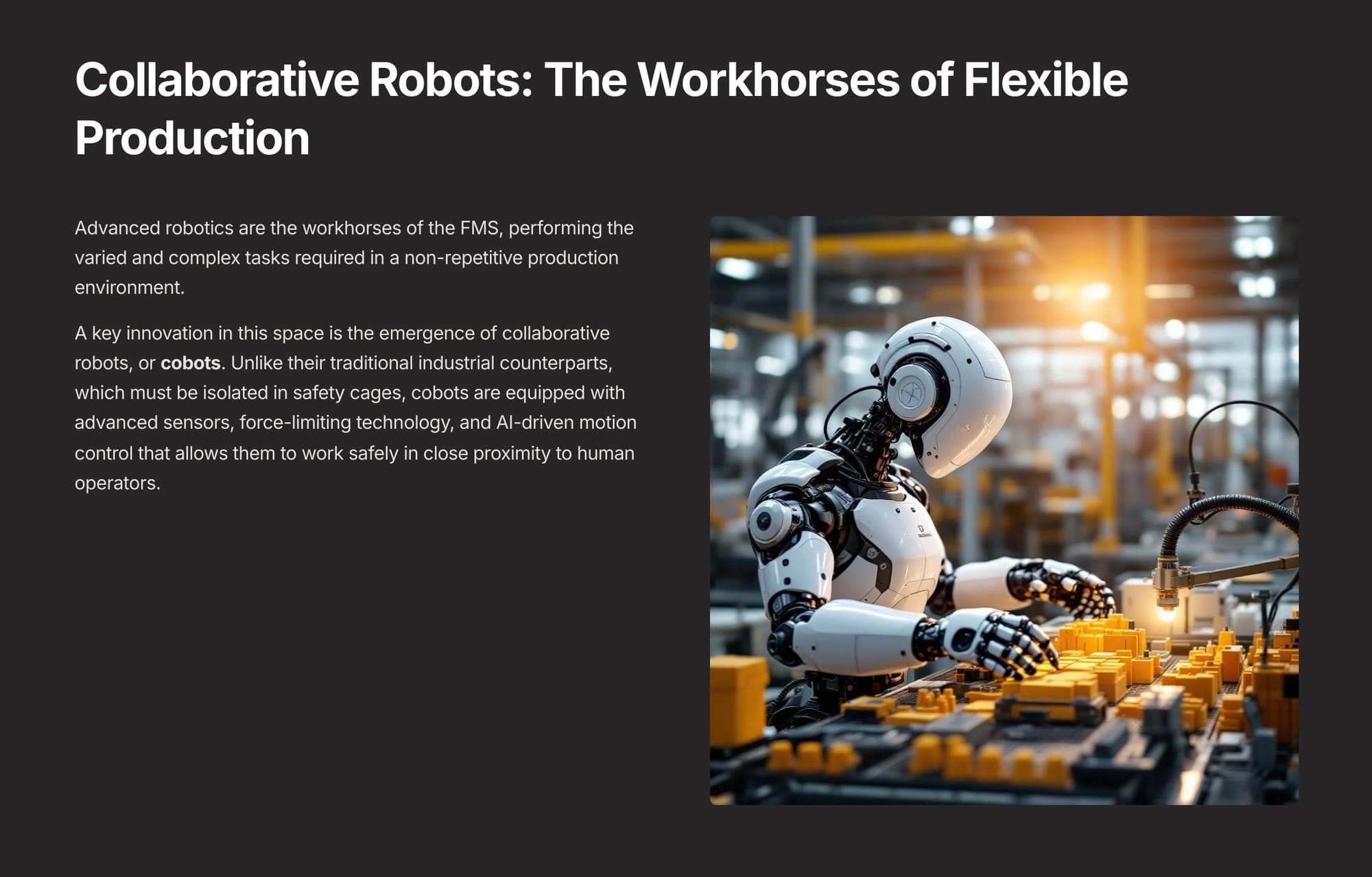
Artificial intelligence (and machine learning act as the intelligent brain of the mass customization ecosystem, transforming both customer interaction and product design. At the front end, AI powers predictive personalization. Algorithms analyze vast datasets to anticipate customer needs and preferences, allowing companies to proactively recommend personalized products or features.
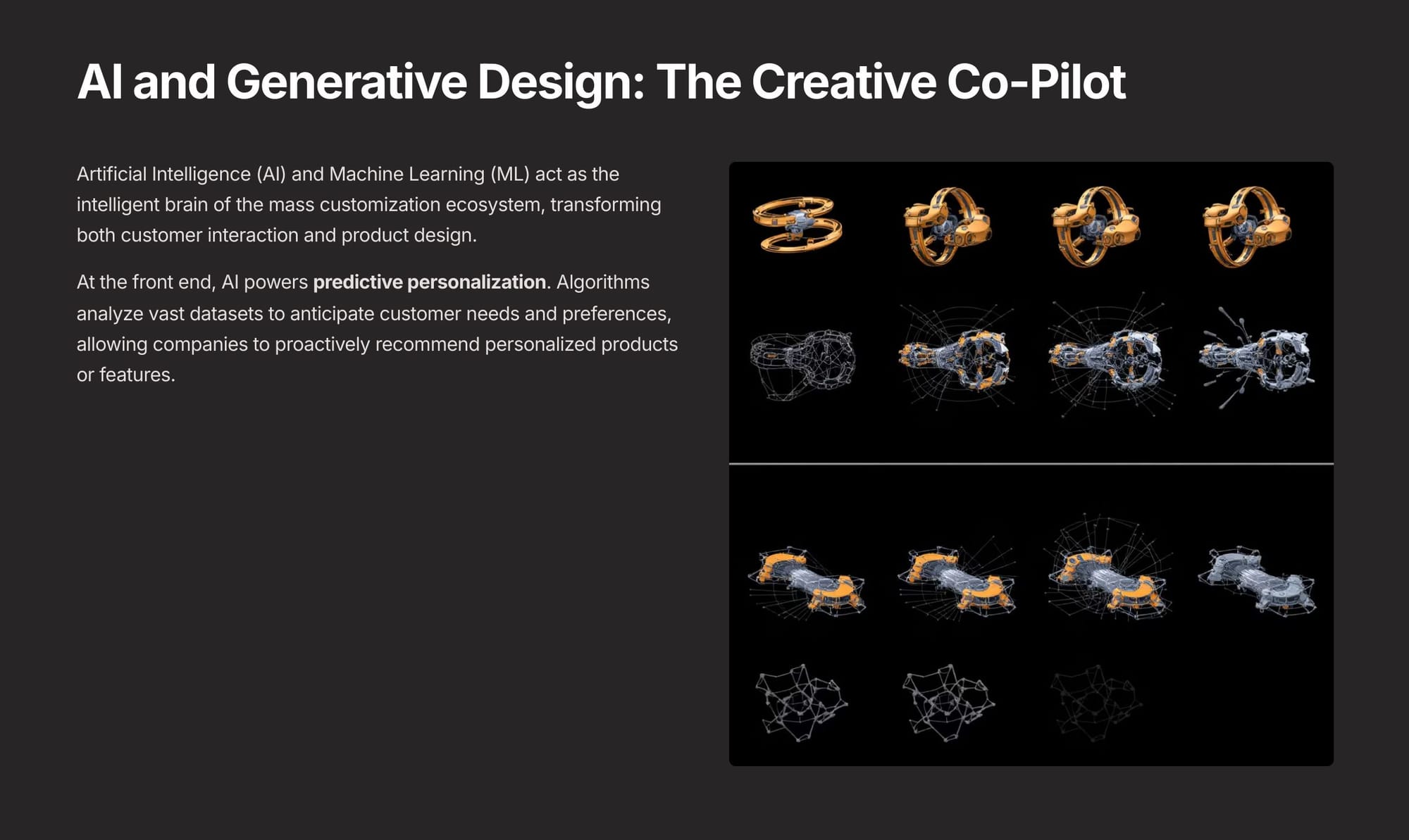
All of this leads to hyper-personalization at scale. Using generative AI, companies can create unique content, packaging, and even product narratives for every individual customer in real-time and at near-zero marginal cost.
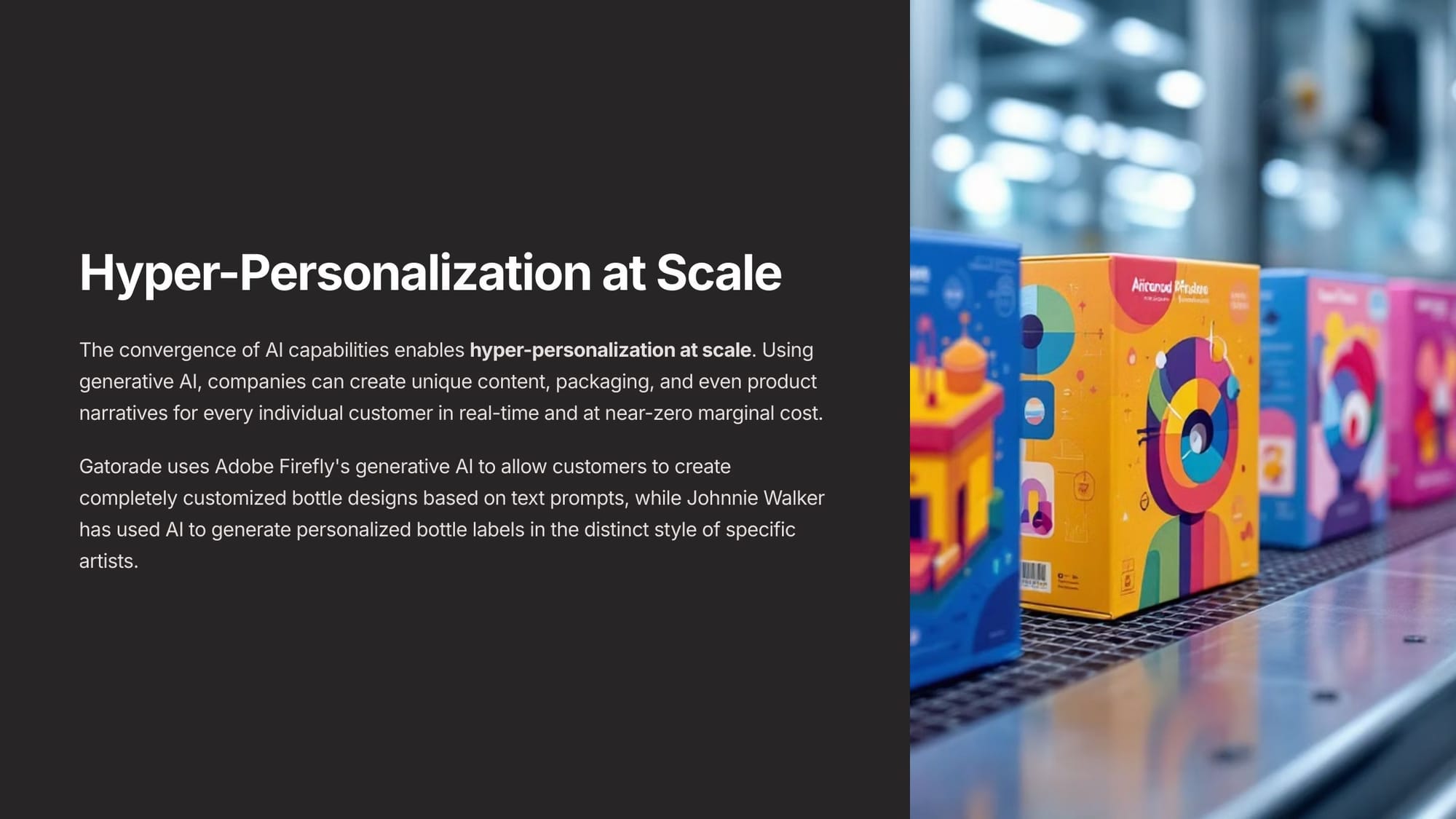
Bringing it all together is the idea of the 'virtual factory' with a digital twin. This provides for a virtual replica of a physical asset, process, or an entire production facility. It is not a static model; it is a dynamic, living simulation that is continuously updated with real-time data from Internet of Things (IoT) sensors on its physical counterpart.
This technology serves as a risk-free sandbox for optimizing the complex operations of mass customization.
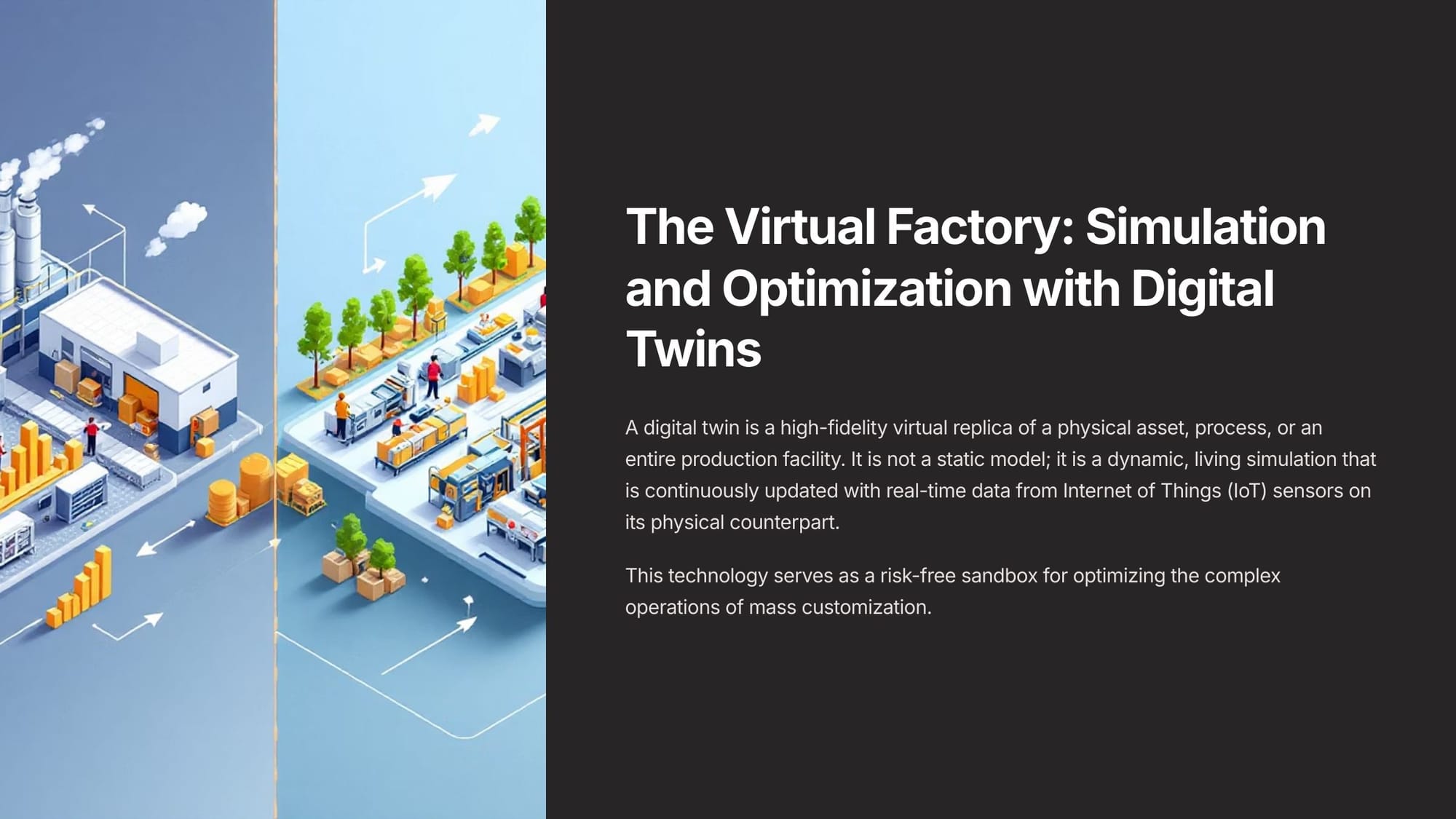
Finally, the ability to customize a product is ultimately constrained by the materials available. Recent breakthroughs in materials science are dramatically expanding the palette for manufacturers. Advanced composites and nanomaterials allow for the creation of products with precisely tailored properties, including exceptional strength-to-weight ratios, electrical conductivity, and thermal stability.
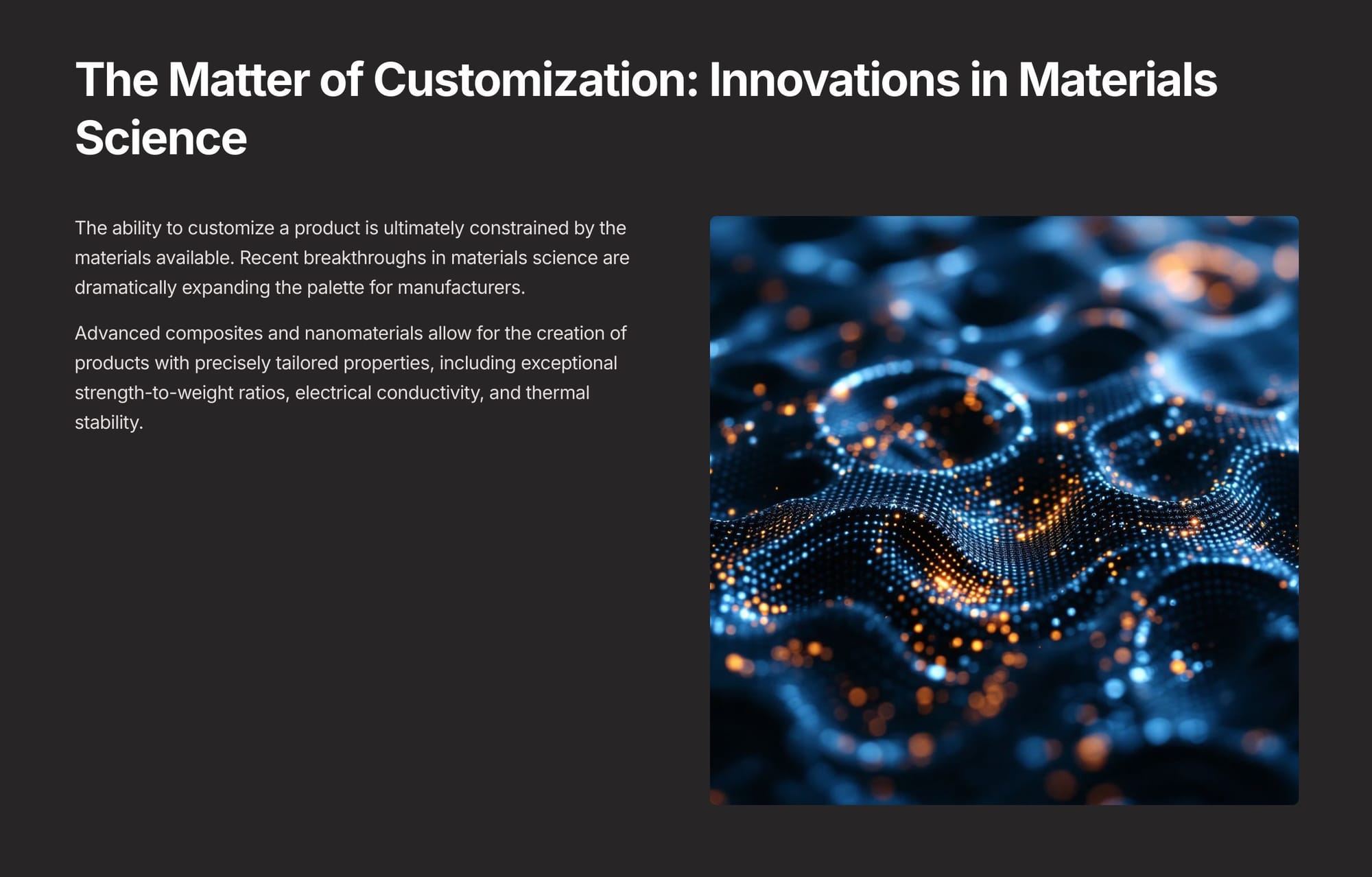
So, how quickly will all this come about? The Technology Maturation Timeline: Phase 1 (2025-2028)will be characterized by the broader adoption and, critically, the integration of currently mature technologies. Companies will move beyond pilot projects to scale up the use of cobots in high-mix assembly lines, implement digital twins for process optimization in specific factories, and refine their D2C product configurators.
The primary challenge and focus of investment will be on solving the complex integration hurdles, building flexible IT architectures, and developing robust data strategies to create a seamless digital thread from customer to factory. Success will be measured by demonstrating clear ROI on a production line or factory-wide scale.
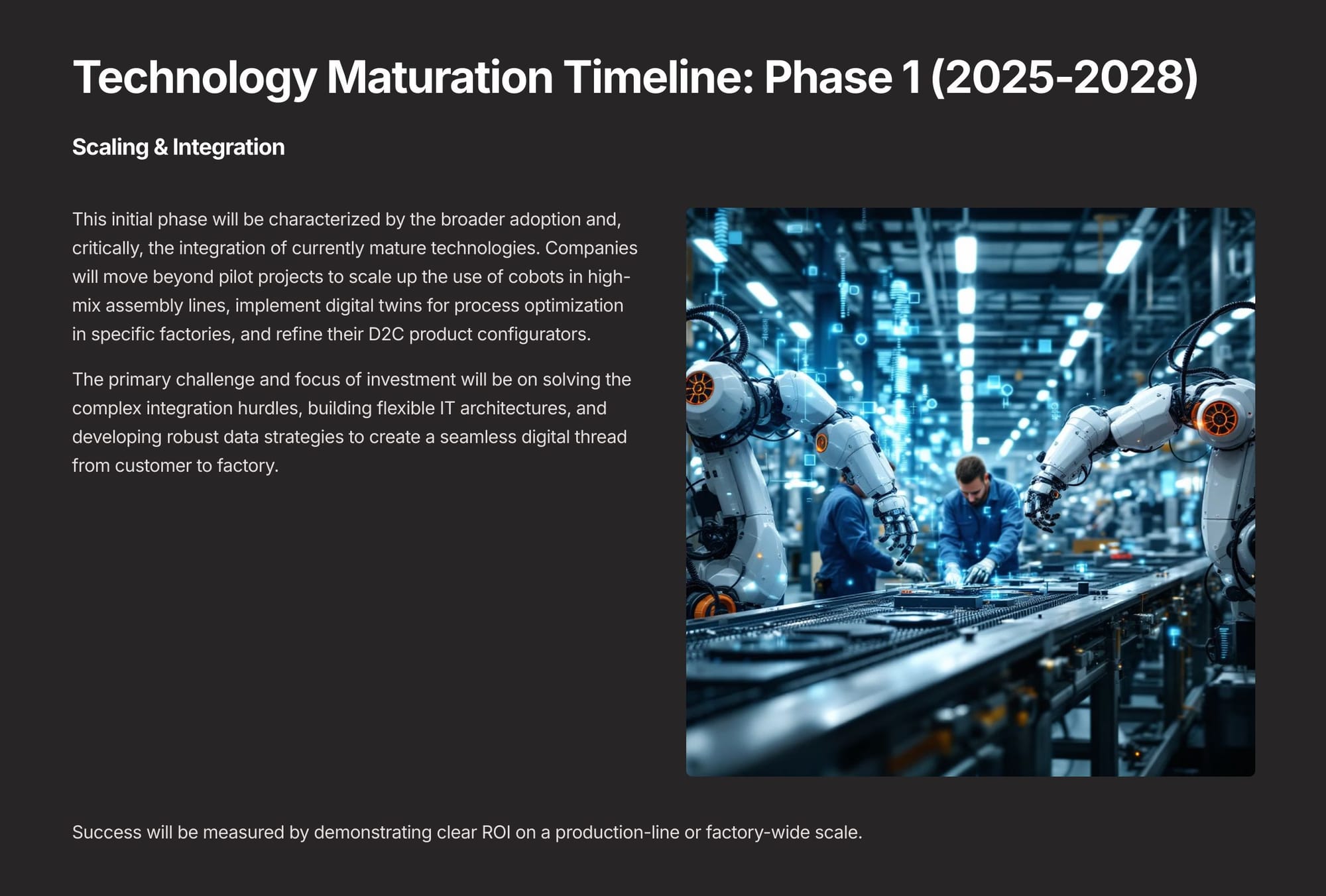
The Technology Maturation Timeline: Phase 2 (2029-2032) will involve a move to intelligence and autonomy, specifically:
- Embedded AI. AI will become a core, embedded component of the manufacturing ecosystem, with generative design shifting from a specialized tool to a standard part of product development.
- Hyper-Personalization. AI-driven hyper-personalization will become common in consumer-facing industries, creating unique experiences at scale.
- Autonomous Production. Within the factory, production systems will gain a higher degree of autonomy, with AI dynamically managing scheduling, logistics, and quality control in real-time.
- Smart Materials. First niche consumer applications of smart materials, allowing for the customization of a product's function, not just its form.
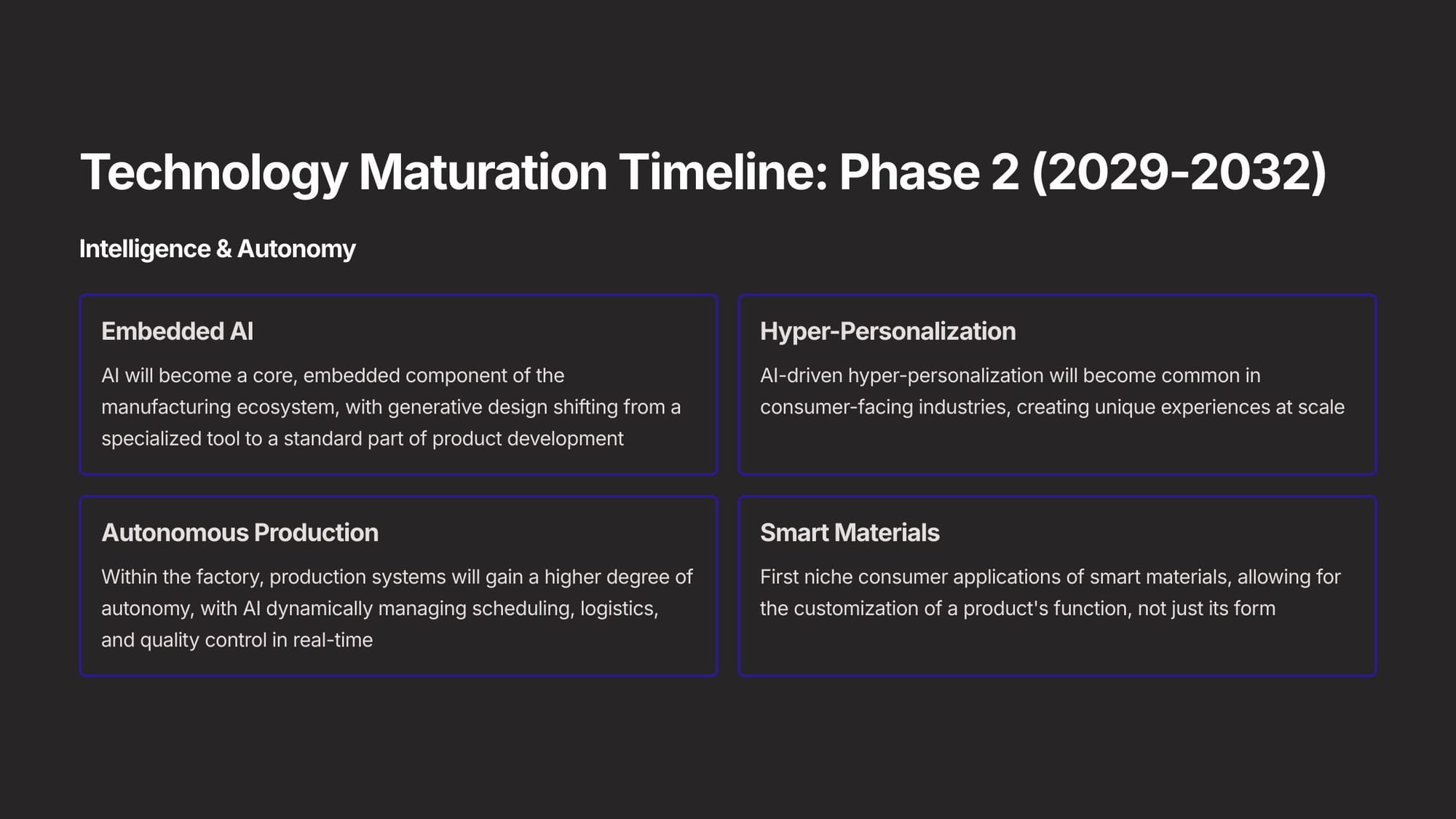
Finally, the Technology Maturation Timeline: Phase 3 (2033-2035)will enable a shift in the structure of manufacturing itself. This phase will see the rise of decentralized networks of highly automated microfactories. Production will become increasingly localized and on-demand, fundamentally reshaping global supply chains and reducing reliance on centralized, large-scale facilities.
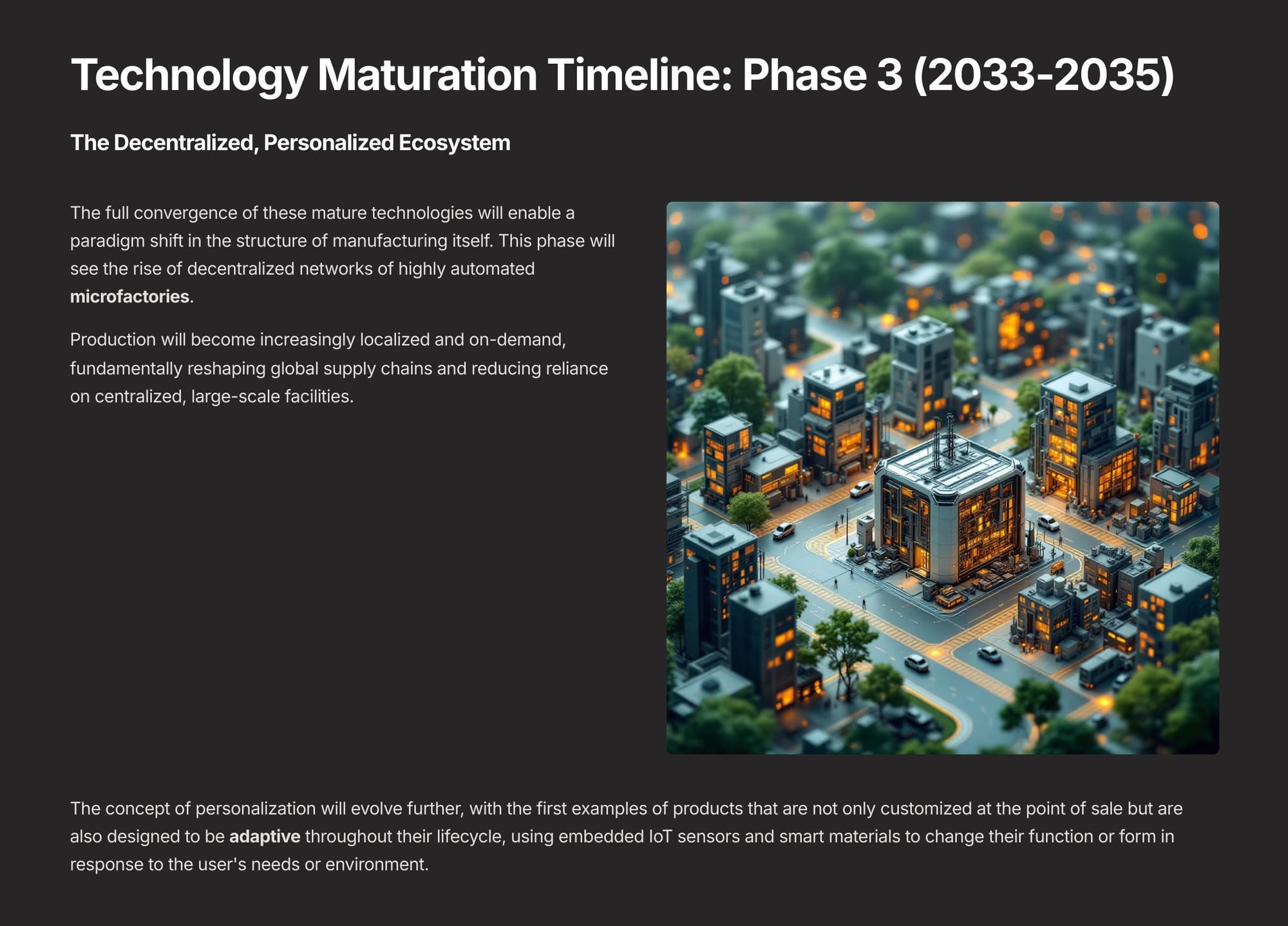
The concept of personalization will evolve further, with the first examples of products that are not only customized at the point of sale but are also designed to be adaptive throughout their lifecycle, using embedded IoT sensors and smart materials to change their function or form in response to the user's needs or environment.
This is a HUGE trend - a MEGA trend - with profound implications. I need not mention that this doubles down on the fact that 'the old jobs aren't coming back because new ones are being created.' Mature societies will succeed; immature, infantile societies will fail.
Futurist Jim Carroll first covered these trends at a major manufacturing conference in Las Vegas in 2005. At that time, they seemed futuristic, out of reach. Today, these trends are coming together.